Asset Leasing and Inspections Streamlined with MobiWork
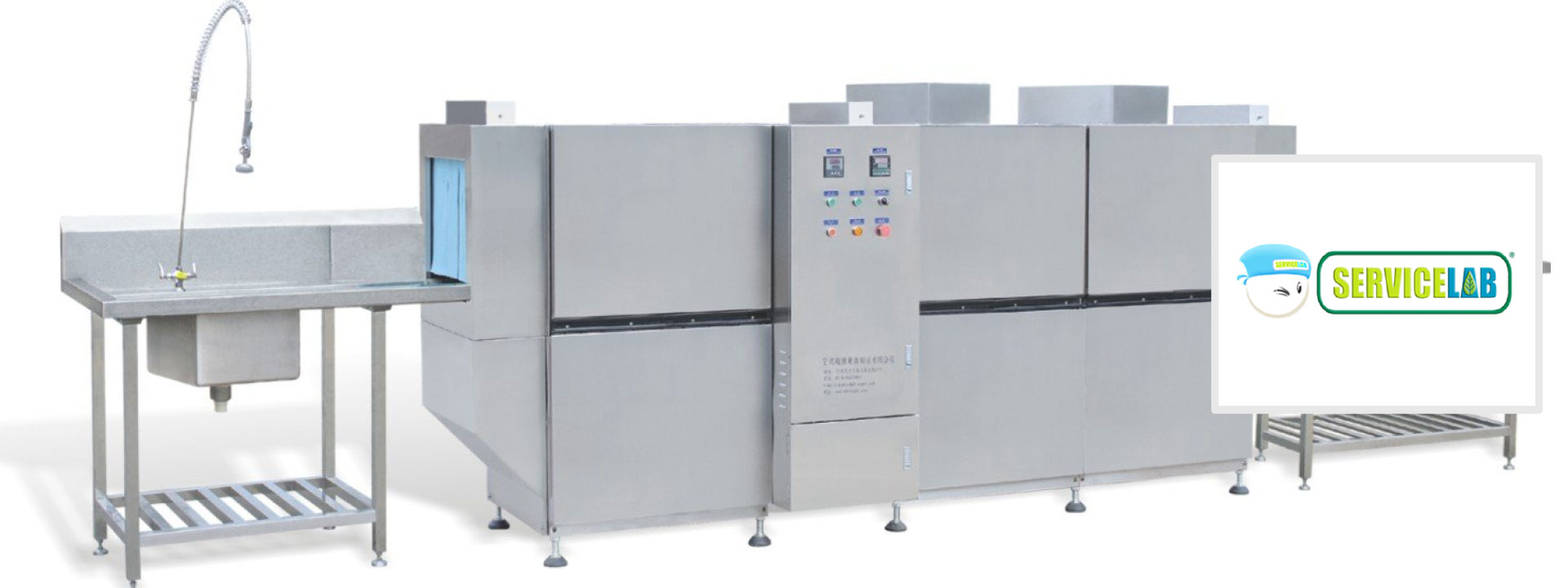
Industry:
Supply Chain Management and Chemical Industry
Regions:
North America
Key Facts:
- 10+ years of experience in the chemical industry
- Over 700 customers
- Over $1 million in tangible assets
Headquarters:
Montreal, Canada
Website:
ServiceLabCanada.com
ServiceLab is a leading industrial dishwasher equipment and chemical supplier for many industries. ServiceLab, located in the heart of Montréal, Canada, has many years of experience in the chemical industry, focusing on cleaning systems and kitchen sanitation. ServiceLab provides, leases, and maintains service equipment for over 700 companies. Their products include industrial grade dishwasher equipment, kitchen sanitation, housekeeping products, dilution systems, chemical pumps and product dispensers. ServiceLab services restaurants, spas, gyms, education facilities, hospitals, and retirement homes. With more than 700 customers and over 1 million in assets installed and managed in the field, ServiceLab strives to be the best dishwasher equipment and chemical provider in the greater Montréal area.
Key Challenges: Asset Leasing, Service Time & History
ServiceLab has approximately 500 assets in the field. Their average asset costs about $6,000 and range up to $25,000. ServiceLab runs a lean operation with an above average amount of transactions. This high volume, low overhead model can sometimes lead to a challenge when managing asset leasing, tracking, and capturing data in the field. For example, because service technicians install equipment at a high growth rate, paperwork could sometimes be lost, not entered and/ or not reported in the system. The admin really wanted a solution that included electronic forms to capture information and signatures, work order management, custom PDF rendering forms, and a detailed product catalog.
Prior to installing MobiWork, ServiceLab was using a hybrid system of outdated software, Excel spreadsheets and manual entry for tracking service. Often times, some equipment received routine servicing, but it was not recorded or tracked correctly, costing valuable time and money every time a machine needed to be inspected or repaired. The servicing schedule was identified as a potential area for improvement; specifically, a better record keeping and invoicing system was needed.
A second issue regarding service was the tracking of specific repairs needed. This is crucial because if a machine malfunctions, the downtime costs can run as high as $200,000 per day. Before, when a technician was sent out, pictures were taken using the technician's cell phone. The photographs then needed to be uploaded to the central database, which did not always go smoothly. The management team needed a solution that could record custom readings, store service notes including date of visit and technician involved, make pictures easier to find and share, store barcodes, QR codes, serial numbers, and send appointment reminders and other notes to customers.
Results: All Assets Tracked & Work Orders Streamlined
ServiceLab has been with MobiWork since 2011, and has decided to stay with MobiWork. ServiceLab's requirements and concerns were easily addressed, in particular, MobiWork's ability to have unlimited customizable fields for capturing specific readings and information, such as the custom form renderings. ServiceLab also wanted to manage their inventory using the product catalog internally, allowing them to save exponential hours in the back end of office operations. David Budman, the Director of Operations at ServiceLab, recently stated, "As our work orders continue to grow, and we add additional customers, we have the flexibility to scale with MobiWork and adapt with MobiWork as we grow".
After deployment of MobiWork MWS, ServiceLab saw immediate turnaround and status of their assets. All of ServiceLab's assets are now tracked, work orders have been streamlined, and their operations efficiency has increased by 78%. Before MobiWork, technicians arrived on site and recorded information by hand, risking paper records being lost in the field. With MobiWork, technicians simply open the app on their smartphone, and enter in specific numbers, readings, snap a picture, and capture a signature, which is all translated immediately and seen in real-time. If specific parts are needed, the technician can use the internal parts catalog to order the necessary parts to repair the equipment. ServiceLab is so thrilled they're now finally able to efficiently and precisely keep track of their asset and service history, and for the first time, are able to scale and grow their successful operations.