Carolina Filters Doubles Audit & Inspection Services with MobiWork
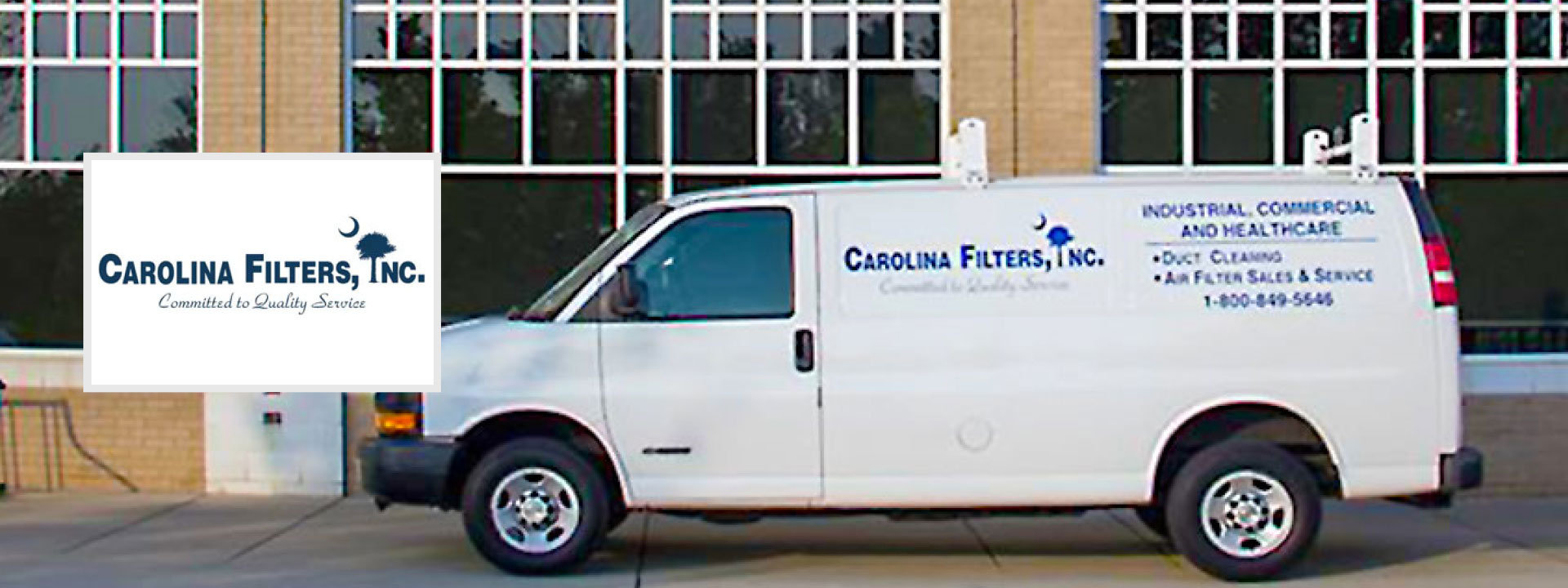
Industry:
Audit & Inspection Services - Primarily for healthcare facilities
Regions:
United States
Key Facts:
- Over 100 employees
- 50 years' experience
Website:
carolinafilters.com
Carolina Filters is an industry leader of indoor air quality, parts cleaning, and process equipment cleaning in South Carolina, North Carolina, and Georgia. (Their Process Equipment Cleaning division has a global customer base while their Indoor Air Quality division is regional/throughout the Southeast.) They specialize in engineered cleaning solutions for industrial, healthcare, universities, and commercial customers with a strong focus in healthcare facilities and nursing homes. Their Indoor Air Quality Division offers HVAC System Cleaning, Air Filter Service and Sales, Overhead Cleaning, Combustible Duct Cleaning, Air Duct Cleaning, Fire Damper Inspections, and more.
Key Challenges: Inadequate Software, Connectivity Issues
With Carolina Filters' Indoor Air Quality Division being a full-service company, they have many different types and amounts of work orders. One of the main services they offer are fire damper inspections, which legally need to take place every 4-6 years. Carolina Filters was in need of a software system that works, and one that the technicians found easy to use. They needed something customizable and flexible enough to make customs forms and reports that export to excel seamlessly. The previous web software system they used did not sync properly, which resulted in many inconveniences. They were constantly having connectivity issues and couldn't work offline, which was a major problem because they often were doing inspections in basements and other spaces where getting service isn't easy, and even walking through hospitals and other facilities with no cell reception. The technicians were having difficulty uploading required pictures to complete a work order, difficulty modifying entries, as well as difficulty tracking things and making changes in the system when necessary. It was slow, cumbersome on phones and tablets, and though it had the additional capabilities that a smartphone brings such as pictures, capturing signatures, and locations, the syncing issues delayed their processes.
Results: Ease of Use, Increase in Daily Inspections, Accuracy
Carolina Filters was impressed by how much MobiWork has to offer and how much it is capable of doing. It was also such an easy onboarding process and they were able to get going with it right away. Though the technicians were a bit apprehensive to switch to a new software, they knew it was imperative. As soon as they did a trial with MobiWork, they were hooked and immediately asked when they could start using it for real and for the long haul. "The support we received from the very beginning of the onboarding process to live deployment has been exceptional. If we ever have a question, we don't hesitate to ask the MobiWork team and they either give us a response immediately or point us in the right direction to solve our problem." The technicians can now fill out forms, take their necessary pictures at a job site, and upload them to MobiWork frustration free. Then they are able to export those photos to excel. Carolina Filters also experienced an increase in productivity, and the reports from these inspections take so much less time to upload. They are also extremely easy to read from an internal point of view, as well as from a customer point of view. In addition, previous PDF forms were only able to show 3 inspections per page, whereas now they can fit up to 11 per page. They no longer have to print these out and waste paper; they are able to email them because they are smaller and more concise with a cleaner view. "Increase in productivity by the technicians has by far been the most important improvement using MobiWork, as well as the accuracy of keeping track of the inspections when working in the field, to being able to access and view everything reported back at the office."